-
Processing equipement
Particle Research Facility has many powder processing equipements, including mixer, fine grind mills, sieves, classifiers, extruder, coating and dryers,
which can be used for powder processing, classifying and size reduction for chemical, pharmaceutical, food, mineral, plastics and cosmetic applications.
-
High Sheer Mixer
Lödige Papenmeier High Sheer Laboratory Mixer
The Lödige high sheer mixer operates on the principle of friction mixing in batch processes. Homogeneous mixing is achieved in a very short time and by extending the processing time precision heating of all particles is obtained. The high speed mixing impeller in special, geometric design accelerates the mixing product both radically to the outside and upwards in a spiral to produce a distinct vortex. The combination of this three-dimensional product movement and the introduction of intensive friction provides targeted, uniform heating of the entire batch. The temperature control can be using in bonding applications for powder coating, and compounding of thermoplastics.
Features:
- Maximum mixing precision and versatility
- PLC/PC control systems for reproducible processes
- Gentle product handling
Reliable scale-up
Air Classifying Mill (ACM)
The Air Classifying Mill (ACM) operates on the principle of impact grinding. Particle size reduction is achieved in these mills through the impact of the particles with the high speed rotating pins and fixed liner. Particle-to-particle collision also contributes to the particle size reduction. During milling the fine particles are carried out by the air circulating in the mill, while coarse particles remain in the mill. The particles are carried to a classifier where the ultrafine particles are passed through a pipe to a baghouse, and the remaining fine particles go to a rotary-sieve where final particle separation occurs. Cut sizes are accurately controlled by varying the classifier speed.
Features:
Very Narrow Particle Size Distribution
One pass milling resulting in accurate particle size cut points that are instantly adjustable and narrow particle size distribution.
Fine Grinding Capabilities
Particle can be grinded down to about 10 microns in one pass.
Minimum Material Contamination
Internals of the mill are easily removed and cleaned making material changeover easy, and hygienic.
Spiral Jet Mill:
The PRF has two different Spiral Jet Mills that are ideal for laboratory applications, and the processing of small batches of material. Jet Mills achieve particle size reduction through particle-to-particle and particle-to-wall collisions using high velocity air nozzles. Powders can ben milled with a large percentage of ultrafine (0.5 to 20 micron) particles produced.
Opposed Jet Mill:
Opposed Jet Mills are engineered to consistently produce ultrafine powders without oversize particles resulting in narrow particle size distributions. Size reduction in an opposed jet mill is achieved exclusively by particle-to-particle collisions. The unit includes a high speed internal classifier ensures tight top size control without over grinding. During the process the ground product is transported to the classifier in an upwards air flow, the final product enters into a collector through the fine material discharge, while the coarse materials returns back into the product bed for further size reduction. This mill is also capable of producing powders with particle size averages as low as 1 - 2 microns, with a large percentage of particles in the 0.5 - 5 micron range.
Turbo-Screen Air Classifier:
The Turbo-Screen Classifier provides continuous, precise screening of dry materials, especially in the finer particle sizes. It provides a highly efficient separation of particles ranging from 850-70 microns. Handles the most difficult materials, including electrostatic materials and particles that tend to agglomerate easily.
Rotary-Sieves:
The Rotary Sieve is a versatile processing equipment that could be used to separate solid particulate materials in a very large range of particle sizes. Large quantity of powder can be separated quickly. The system has relatively low energy consumption and is an attractive size separation technology for the food, pharmaceutical, plastics, and powder coatings industries.
Ultrasonic Vibrating Sieves:
PRF is equipped with three ultrasonic sieves of different sizes including an 8", 12", and 22" unit.
8" Ultrasonic Sieve - The small 8" laboratory scale ultrasonic sieve is ideal for small quantities of powders requiring highly accurate separation with maximum powder recovery.
12" Ultrasonic Sieve - The VORTI-SIV RBF-12 comes with a 12" diameter screen and is the most advanced small batch sieving machine on the market. The units use a unique gyratory screening-action generated by an adjustable off-balance flywheel, which is powered by a direct drive 1/2 HP, 3450 RPM motor. Any point on the screen surface moves in a circular orbit, but the screen itself does not rotate. Vorti-Sieve is equipped with a 50kHz, 110/120 volt ultrasonic transducers. Ultrasonic energy is directly applied to the wire mesh screen via the transducer plate. This breaks surface tension, making the stainless steel mesh free of friction and helps to de-agglomerate particles and eliminates particle blinding. T
22" Ultrasonic Sieve - The 22" ultrasonic sieve is ideal for large quantity powder processing applications. The ultrasonic energy produced by the transducer eliminated particle blinding of the screen and allows for efficient sieving of a large quantity of powder in a continuous manner.
Twin-screw extruder
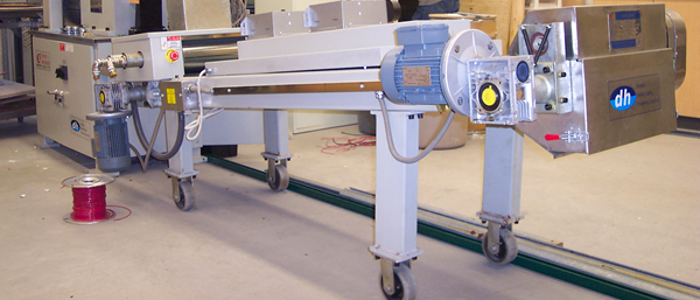
Twin-screw extrusion is used extensively for mixing, compounding, or reacting of polymeric materials. At PRF we have a high-speed co-rotating twin-screw extruder. The processing section of the unit is made up of several modular barrel sections which house the two co-rotating screw shafts. The barrel sections and screw elements can be freely combined so as to get an optimal arrangement matched specific processing needs.
Extruder Specifications: Thorough Put: 40 Kg/hr, Screw Diameter: 30 mm, Length/Diameter Ratio: 16, Main Motor: 7.5 kW, Screw Speed: 0 - 600 rpm, Feeder Motor: 0.12 kW, Heating Power: 3.2kW.
Conveying Elements - The high-speed twin screw shaft is composed of shaft with spline or key, screw bushings for conveying and extrusion and kneading blocks for dispersion and homogenizing. The configuration of screw bushing and kneading block is changeable. High volume feed elements for the screw shafts provide improved material intake for materials with poor feeding characteristics.
Kneading blocks and Dispersive Mixing Elements - The mixing and kneading elements are designed in a variety of lengths, pitches and pitch direction. The result is precise shear, melt and energy control plus homogeneous mixing of the melt and dispersion additives. The machine can be fed with powder, pellets, chips, glass fiber, pastes and liquids.
Electronic Control Box - The high performance electronic control box in this unit has the advantages of high reliability, good comprehension, compact structure, and can lock the major technology parameters with cipher code.
Extruder Barrel with heating/cooling units - There are a total of three heating/cooling zones in the extruder barrel.
Powder Coating Equipments
The Particle Research Facility (PRF) has been involved in powder coatings research and formulation for more than seven years. The research at PRF has led to a number of novel powder coatings inventions and a patent on a novel ultrafine powder coatings technology. The ultrafine powder coatings result in thinner films, smoother surface and leads to considerable cost savings to the powder coating industry. Dr. Jesse Zhu is involved with a number of industrial collaborations for developing and transferring this technology. Furthermore, we are fully equipped to develop novel powder coating formulations for specific application requirements.
Nordson 902 Powder Coating Booth:
The model 902 powder spray booth provides clean, efficient and flexible operation in batch, short-run and custom-color manual powder coating operations. With Nordson cartridge-filter technology, the booth provides high material utilization and fast, color-change capability in a compact, modular system that is ideal for use in laboratory and manual reinforcement applications.
In-House Designed Powder Coating Spray Booths:
At PRF we have build two different sized powder coating spray booths for powder coatings application, formulation, and modeling research.
- Large in-house designed spray booth: 2 m x 1.8 m x 1.6 m
- Small in-house designed spray booth: 1 m x 0.8 m x 1.2 m
Portable Powder Paint Spray Systems:
At PRF each of the three above spray booths have it's corresponding portable powder paint spray systems. There are two Spray system to choose, one is Sure Coat Manual Spray Gun Systems from Nordson and the other is OptiFlex Manual Spray system from ITW Gema.
- 1. Sure Coat Manual Spray Gun Systems: The Nordson Sure Coat system provides operator-selectable, product-specific coating modes that deliver optimal coating performance for a variety of different powder coating applications. The system allows the user to choose the ideal application parameters for high levels of coating quality, efficiency and consistency.
Features:
Constant-read gauges on the control display air-pressure and electrostatic parameters even when guns are not triggered on
Self-diagnostics feature reduces downtime, minimizes rejects and facilitates troubleshooting
Purge button on gun handle allows operator to spray air to minimize powder build-up and surging
- 2. OptiFlex Manual Spray System: The OptiFlex system combines flexibility and economy, and is ideal for medium to large production runs. The system stores your application settings for easy recall in any coating scenario.
Features:
"On-gun" remote controls adjust coating mode and powder delivery without requiring operators to turn away from their work
OptiStarT Advanced Control Unit provides total control flexibility, giving operators a choice between 20 custom programs and 3 pre-programmed settings
Patented Digital Valve Control (DVC), automatically and precisely adjusts all air required for powder coating
Büchi Mini Spray Dryer B-290
Spray drying is the most widely used industrial process involving particle formation and drying. The spray drying technique involves the atomization of a liquid feedstock into a spray of droplets and contacting the droplets with hot air in a drying chamber. The sprays are produced by either rotary (wheel) or nozzle atomizers. Evaporation of moisture from the droplets and formation of dry particles proceed under controlled temperature and airflow conditions.
The Büchi Spray Dryer B-290 signifies a new dimension in research and development. The instrument is capable of producing uniform powders from 50 ml or less of organic or aqueous solutions, in just minutes.
Features:
- Easy to Clean and Sterilize: Automatic nozzle cleaning through manual or preset program and simple nozzle disassembly with easy sterilization
- High Precision: Nozzle fitted with ruby stone to ensure high precision spraying
- Maximum Contaminate-free Yield: High quality inlet and outlet filters ensure maximum yield and contamination-free work
- Electronic Monitoring: Electronic monitoring of pressure, temperature, and oxygen levels
ModulyoD Freeze Dryer
The ModulyoD Freeze Dryer is a multipurpose ice condenser with a five-liter capacity. It is designed to work with a wide variety of drying accessories, including those used for flasks, vials, ampoules and bulk materials. The robust design includes a high quality, smooth wall stainless steel ice condenser with an easy to use, front mounted, bottom drain.
Features:
- Compact bench-top footprint
- Digital display of vacuum and temperature
- CFC Free Refrigeration System